Ultimate Guide to Methyl Methacrylate and Polyurethane Joint Sealant for Jet Fuel Resistance in Airports
- Fuat Akkavak
- Oct 22, 2024
- 3 min read
Methyl methacrylate (MMA) and polyurethane joint sealants are essential for maintaining the safety and integrity of airport surfaces. These advanced materials are engineered to withstand harsh conditions found in aviation environments, including exposure to jet fuel, extreme weather, and heavy traffic. This guide provides a detailed, step-by-step process for cleaning, repairing, and joint filling using these innovative products, emphasizing MMA’s rapid curing properties that enable quick turnaround times.
1. Preparation and Cleaning
Surface Assessment:
Start by assessing the area requiring repair or joint sealing. Common targets include runways, taxiways, and aprons, where structural integrity is crucial.
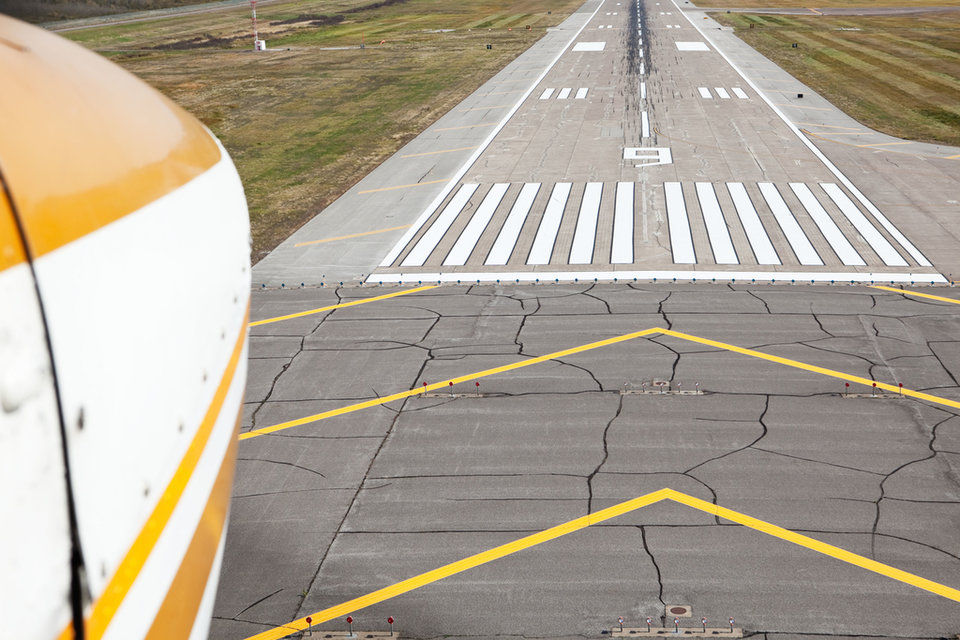
Cleaning Process:
Utilize a high-pressure washer to remove dirt, oil, and contaminants. Pay particular attention to oil stains, as they can impede adhesion.
For stubborn residues, consider using a degreaser or solvent recommended by the manufacturer.
Ensure the area is completely dry before proceeding.

2. Mixing Methyl Methacrylate
Component Preparation:
Measure the MMA components precisely according to the manufacturer’s specifications. Accurate measurements are critical for optimal performance.
Mix the components in a clean container, preferably using a mechanical mixer, until you achieve a homogeneous blend.
(Insert image of MMA components being mixed in a container)
3. Application of Methyl Methacrylate
Filling and Repairing:
Pour the mixed MMA into cracks or damaged areas of the pavement. This can include filling voids or repairing deteriorated sections around expansion joints.
Use a trowel or squeegee to spread the MMA evenly across the surface, ensuring all voids are filled.
Rapid Curing Time:
One of MMA’s standout features is its rapid curing capability. It can cure in as little as 30 minutes, allowing runways to be reopened for aircraft landings within one hour after repair. This efficiency is vital for minimizing downtime and maintaining flight schedules.
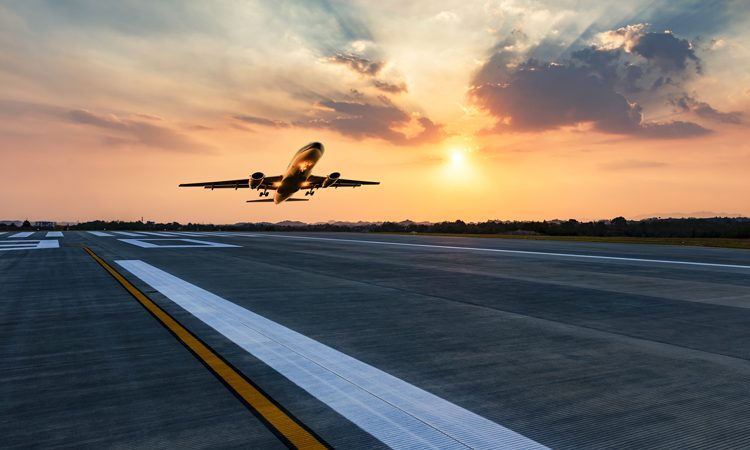
4. Joint Filling with Polyurethane Sealant
Preparing the Joint:
Inspect the joints to ensure they are clean and free of debris. This is particularly important for expansion and contraction joints.
(Insert image of an expansion joint being prepared for sealing)
Application of Polyurethane:
Load the polyurethane sealant into a caulking gun and apply it evenly to fill the joint completely.
Use a spatula or your finger to achieve a smooth finish.
(Insert image of polyurethane being applied to a joint)
5. Finishing Touches
Curing and Setting:
Allow the polyurethane sealant to cure fully, typically taking 24 hours to several days, depending on environmental conditions.
Quality Inspection:
After curing, perform a thorough inspection of repairs and joints. Look for inconsistencies like air bubbles or areas that need additional filling.
6. Application in Airport Environments
Importance of Fuel Resistance:
In airport settings, surfaces are routinely exposed to jet fuel spills, hydraulic fluids, and de-icing agents. Using MMA and polyurethane sealants resistant to these substances is essential for operational safety.
Road Marking and Repair:
MMA products are ideal for road marking applications, providing high visibility and durability crucial for directing aircraft safely.
(Insert image of freshly marked runway lines)
Enhanced Durability:
The combination of methyl methacrylate for repairs and polyurethane for joint filling creates a robust, long-lasting solution that withstands heavy traffic, harsh weather, and chemical exposure.
Conclusion
Utilizing methyl methacrylate and polyurethane joint sealant in airport applications is vital for ensuring the safety and durability of runway and taxiway surfaces. The rapid curing properties of MMA allow for minimal downtime, enabling planes to land just one hour after repairs. By following this unique guide, you can effectively prepare, repair, and fill joints to create surfaces that endure the demanding conditions of aviation environments. Prioritize quality materials and adherence to manufacturer guidelines for optimal results.
Comments